In the field of electronic manufacturing, whether it is products on the market or equipment in the production workshop, we will find a variety of PCB boards, their colors are varied, from common green to rare red, blue, black, etc., which are dazzling. So, what are the uses of these PCB boards of different colors? What kind of mystery is hidden behind them?
The origin and significance of PCB board color
First, let us understand the origin of PCB board color. The color of PCB board is mainly determined by the solder mask on its substrate. The function of solder mask is to prevent solder from flowing freely during welding to avoid short circuit. The color of solder mask can be achieved by adding different colorants, thus forming the colorful PCB board we see.
The role of PCB board color
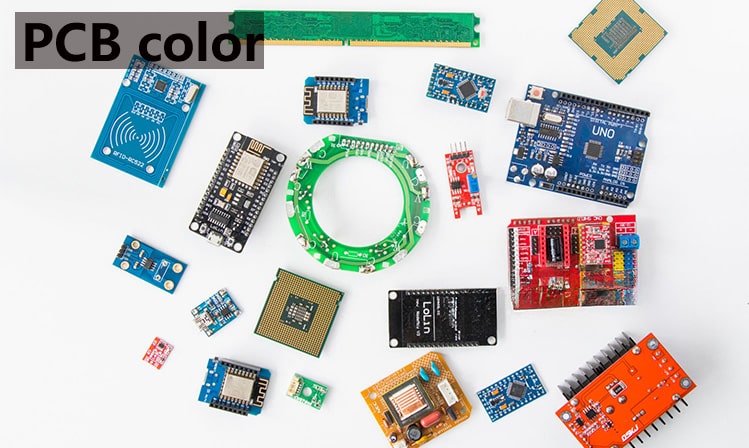
Convenient for production and maintenance: PCB boards of different colors can help workers quickly distinguish different product batches, production processes or special requirements. In the production process, the difference in color helps to achieve assembly line operation and process control; in the maintenance process, color can be used as a reference for fault location to help maintenance personnel quickly find the problem.
Improve the aesthetics: As the core component of electronic products, the aesthetics of PCB boards are also receiving more and more attention. Colorful PCB boards can meet the personalized needs of consumers and add a unique aesthetic to electronic products.
Functional differentiation: In some special application scenarios, the color of PCB boards can also be used as a functional differentiation. For example, in high-density electronic devices, PCB boards of different colors can distinguish different signal transmission paths and improve the overall performance of the equipment.
Reflect the quality of PCB boards: The color of PCB boards also reflects their quality to a certain extent. High-quality PCB boards are usually uniform, full and not easy to fade, while poor-quality PCB boards may have uneven colors, spots or fading, which affects the performance and reliability of the circuit board.
Adapt to special environments: In some special environments, the color of PCB boards needs to be adaptively adjusted. For example, in high temperature, high humidity or highly corrosive environments, choosing colors with better weather resistance and corrosion resistance can extend the service life of PCB boards.
Common PCB board colors and their characteristics
Green PCB board: the most common, with good visibility and recognition, mature manufacturing process, low cost, widely used in various electronic products.
Red PCB board: strong visual effect, often used in high-end or special products, complex manufacturing process, high cost, narrow scope of application.
Blue PCB board: between green and red, relatively simple manufacturing process, moderate cost, widely used in products with cost requirements.
Black PCB board: has good anti-interference ability, is widely used in some equipment that needs to reduce electromagnetic interference, complex manufacturing process, high cost.
When choosing PCB color, it is usually necessary to consider aesthetics, functional requirements, production cost and inspection convenience. If you need to know more about PCB proofing, SMT patch, PCBA processing related technical knowledge, you can follow PCBAMake, welcome to leave a message to get it!